Type |
1 Wire wound heating element embedded in fabric |
2 Zig-Zag heating wires |
3 Wire wound heating element vulcanized inside rubber |
4 Etched metal foil vulcanized inside rubber |
5 Thick film heaters, silk screen printed |
6 Etched foil |
Picture |
|
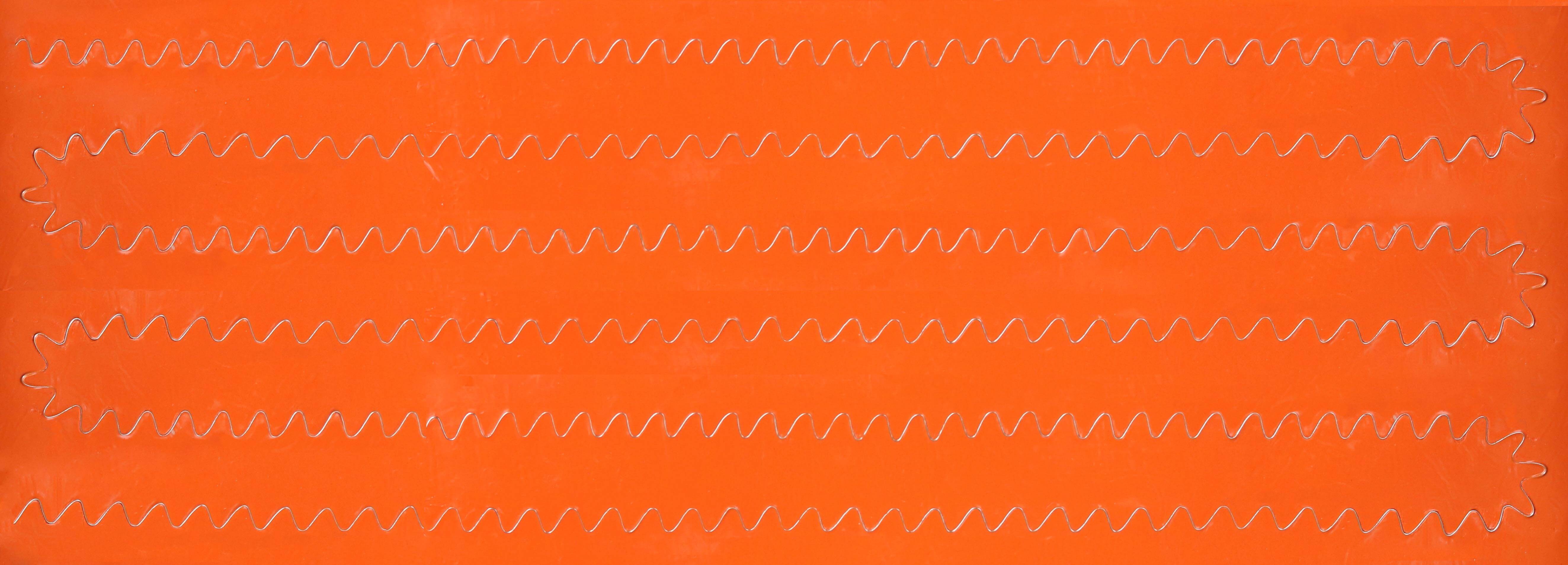 |
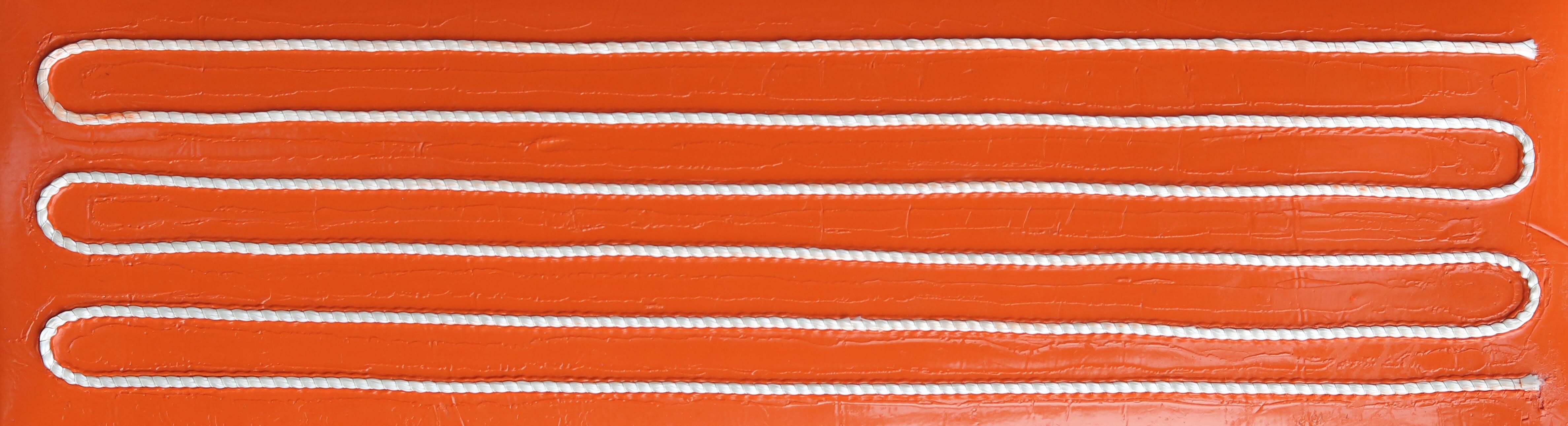 |
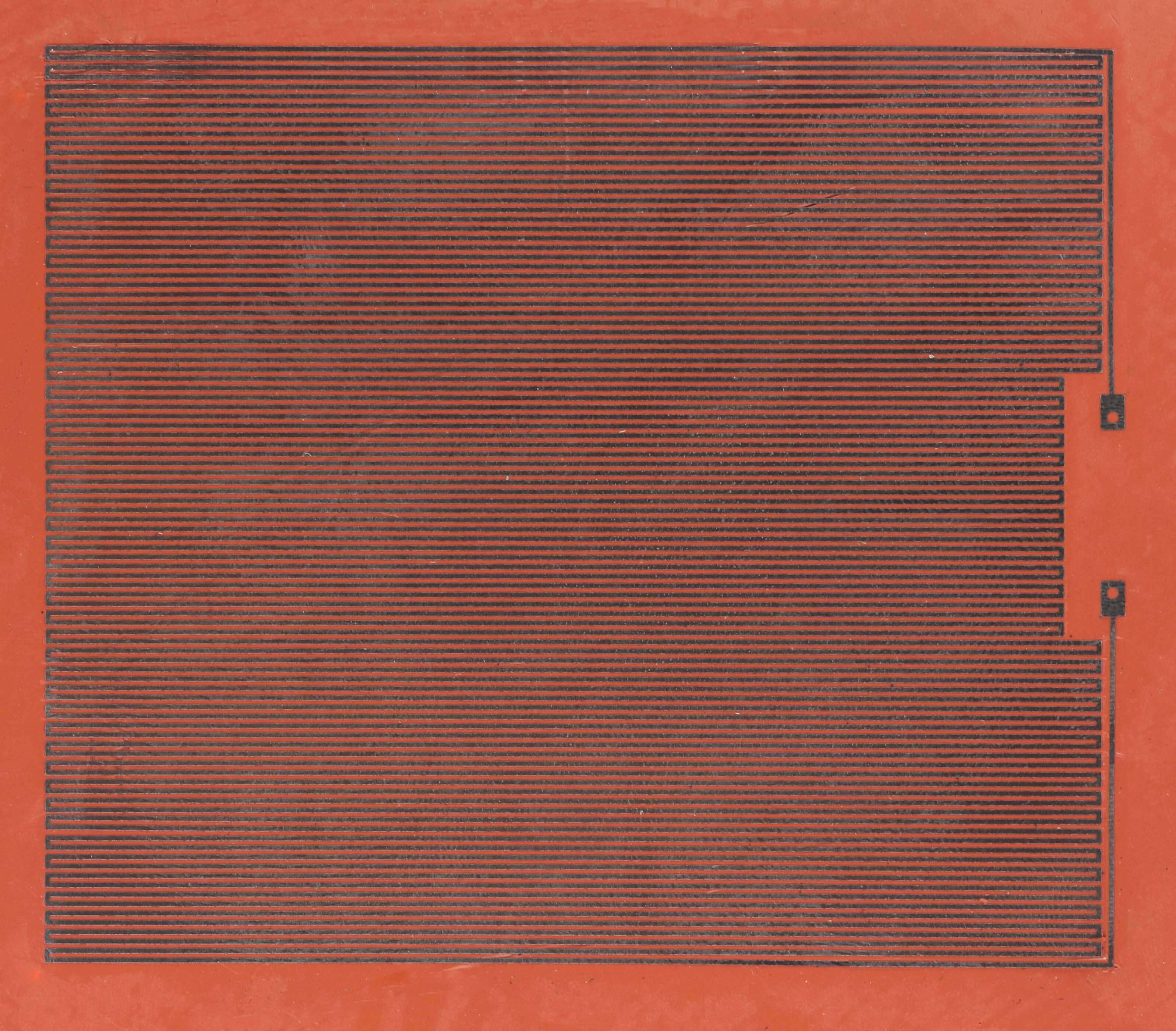 |
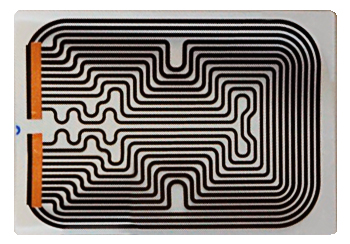 |
|
Temperature range |
-20+120°C . Usual value as it depends of the fabric used and heating wire insulation.
(From -20+120°C for PA66 to -60+350°C for fiberglass or aramide) |
-60°C to 230°C |
-60°C to 230°C. |
-60°C to 230°C. |
-20+80°C. Temperature resistance depends mainly of conductive and resistive inks used.
Insulation foil can be PVC or PET or even polyimide. Surface power load limited
to 0.2W/cm². |
-60 to 230°C. Usual value, as it depends of insulation foil material, adhesive used to
bond the foils and inks. Insulation film can be PET (max 120°C due to film material),
Kapton (max 230°C due to PSA) |
Flexibility |
Good resistance to bending and repeated flexing. |
Limited resistance to bending and repeated flexing. |
The best resistance to repeated flexing. |
Limited to static application because poor resistance to flexion of the metal foil.
|
Very poor resistance of inks to flexion. |
Limited to static application because poor resistance to flexion of the metal foil.
|
Used in |
Industrial jacket heaters.
Domestic and industrial blanket heaters and heating pads.
Heating clothes.
|
Industrial flexible silicone heaters. Low volume applications. |
Industrial flexible silicone heaters, low volume applications
Temperature range from -60°C to 230°C
|
Most of large volume industrial and commercial applications requesting high
temperature resistance and high watt/cm² |
Low cost and low temperature heaters used in automobile for heating seats or mirrors
to keep ice from forming on the side view mirrors of cars, busses and trucks. |
Applications that require a lightweight solution or a rapid heat-up time.
Wide temperature range when using Kapton
|
Technology |
The oldest technology, dating back to the end of 19th century.
The resistive conductor is coiled around fiberglass or aramid core. (It was asbestos
until 50 years ago).
Then the flat heater can be made using 2 technical solutions:
1/- Heating fabric whose warp yarns are made of fiberglass, cotton aramid, polyimide,
and weft yarns are made of this coiled heating wires
2/-Stitching the wires on a fabric. This solution allows to use wires with a primary
insulation in silicone or FEP. Then the primary insulation can receive a metal braid,
for grounding. This is the single way to produce flexible heaters with a
grounding braid, requested in some industrial applications. |
The resistive conductor is formed in a flat zig-zag, and assembled in a web. This
technology produces heaters without thickness increase,similar to the
etched models. The cheapest solution for small quantities, (Technology
patented by Ultimheat) |
The resistive conductor is coiled around fiberglass or polyimide core. Then a web is
made with the coiled wires hand pressed on the un-vulcanized silicone. Then the heating
web is vulcanized between 2 sheets of fiberglass reinforced silicone rubber.
In their traditional time-consuming assembly process, they are only suited
for small quantities. In the Ultimheat patented technology the fiberglass
fabric net and the heating wire are computer designed, and heating wire is
automatically embedded in the fiberglass net before vulcanizing. This
allows fully automated production and large volume applications.
|
The heating element conductive web is made from a thin metal sheet chemically etched
with a technology similar to the printed circuits processing. Then this metallic web
can be vulcanized between 2 flexible and insulating sheets. Sheets can be made of any
type of rubber or elastomers. Because of the larger paths, smaller spacing between
elements and better heat transfer, the power density can be up to 2 time bigger than
classical wire wound models. They are suited for medium and large
quantities. |
Thick film heaters are constructed on silk screening of conductive and resistive inks.
These inks are printed on a flexible substrate. They can be produced using an ink that
makes the heater capable of self-regulating its temperature or as a fixed resistance
heater. |
Etched foil Kapton flexible heaters are made with a thin metal foil as the resistance
element. The resistance pattern is designed in CAD and transferred to the foil in a
process similar to the printed circuits manufacturing. The metal foil is then laminated
and bonded to the insulating substrate with adhesive (FEP or Acrylic). The metal
foil/substrate is then processed through an acid to produce the etched heating element.
The top layer is then added and bonded and laminated with adhesive as done for the
first side. Polyimide heater offers dimensional stability and high tensile strength. It
is also resistant to most chemicals. (Kapton is a brand name from Dupont for
polyimide). |